Lean Manufacturing is a systematic approach to improving efficiency and eliminating waste in production processes while delivering maximum value to customers.
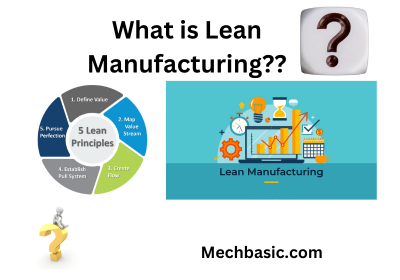
In this article
- What is lean manufacturing?
- Core principles of Lean Manufacturing.
- 7 types of wastes.
- Lean Manufacturing Tools.
- Lean Manufacturing Examples.
- Benefits of Lean Manufacturing.
What is lean manufacturing?
Lean Manufacturing is a systematic production methodology focused on minimizing waste (non-value-added activities) while maximizing value to the customer. It emphasizes continuous improvement, efficient resource use, and the creation of streamlined processes to deliver high-quality products or services at the lowest possible cost.
Core principles of Lean Manufacturing
Value Identification
- Identify what the customer values in the product or service. Any activity not contributing to this value is considered waste.
Value Stream Mapping (VSM)
- Map out the entire process of creating the product, identifying waste and inefficiencies in each step.
Flow Optimization
- Ensure a smooth and uninterrupted workflow by removing bottlenecks, reducing cycle time, and standardizing processes.
Pull System
- Produce only what is required based on customer demand, avoiding overproduction. Tools like “Kanban” help regulate this process.
Continuous Improvement (Kaizen)
- Foster a culture of continuous, incremental improvement to achieve long-term efficiency.
7 types of wastes.
Lean manufacturing identifies seven major forms of waste (known as “Muda”):
- Overproduction – Producing more than is needed.
- Waiting – Idle time caused by delays or bottlenecks.
- Transportation – Unnecessary movement of materials between locations.
- Overprocessing – Adding features or steps that don’t add value.
- Inventory – Excess materials or products that are not yet sold.
- Motion – Unnecessary movements by workers or machines.
- Defects – Products or components requiring rework or scrapping.
Lean Manufacturing Tools.
Kanban
- Visual scheduling system that signals when to start or stop production.
- Example: A card-based system is used to manage inventory in real time.
5S System
- A workplace organization method:
- Sort (Seiri): Remove unnecessary items.
- Set in Order (Seiton): Arrange tools and materials for easy access.
- Shine (Seiso): Keep the workspace clean.
- Standardize (Seiketsu): Establish consistent procedures.
- Sustain (Shitsuke): Maintain discipline.
Kaizen
- Continuous improvement involving small, incremental changes led by employees.
Just-In-Time (JIT)
- Producing only what is needed, when it is needed, to reduce inventory and waste.
Poka-Yoke
- Error-proofing systems designed to prevent defects.
- Example: Color-coded connectors that prevent improper assembly.
Value Stream Mapping (VSM)
- A flowchart method for analyzing and improving the steps in a process.
Heijunka
- Production leveling to balance workload and reduce fluctuations in demand.
SMED (Single-Minute Exchange of Die)
- Reducing setup times for machines to less than 10 minutes, enabling faster production changeovers.
Lean Manufacturing Examples.
The following are some of the examples of Lean Manufacturing.
- Toyota Production System (Automotive Industry).
- Amazon (E-commerce Fulfillment)
- Nike (Apparel)
- Food and Beverage Industry(McDonalds)
- Electronics Manufacturing(Dell).
For full detailed information of these examples click Lean Manufacturing examples.
Benefits of Lean Manufacturing.
- Reduced production costs and waste.
- Increased productivity and efficiency.
- Improved product quality and customer satisfaction.
- Shorter lead times and quicker delivery.
- Enhanced worker safety and morale.
Conclusion
Lean manufacturing is more than just a set of tools or techniques; it is a philosophy that prioritizes efficiency, quality, and continuous improvement. By systematically eliminating waste and focusing on delivering value to the customer, lean manufacturing helps organizations reduce costs, improve productivity, and enhance customer satisfaction.