Lean Manufacturing and Six Sigma are two complementary methodologies aimed at improving efficiency and quality in manufacturing and business processes.
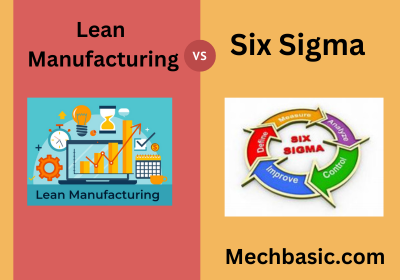
Contents:
- Definition.
- Purpose.
- Principles
- Tools and Technique.
- Focus areas.
- Metrices.
- Industrial applications.
- key Differences.
- Common similarities.
- When to use.
Definition:
Lean Manufacturing:
Lean Manufacturing is a systematic approach to improving efficiency in production and business processes by eliminating waste and focusing on value creation. It aims to deliver the maximum value to customers with minimal resources, ensuring smooth workflows and cost efficiency.
Six sigma :
Six Sigma is a data-driven methodology and management approach aimed at improving the quality of processes by identifying and reducing defects, errors, or variability. It uses statistical tools and techniques to systematically improve process performance, reduce costs, and enhance customer satisfaction.
Purpose and Focus
- Lean Manufacturing: Focuses on eliminating waste and improving flow in processes to deliver value to the customer more efficiently. The main goal is to improve speed and reduce non-value-adding activities.
- Six Sigma: Focuses on reducing process variation and improving quality by identifying and eliminating defects. The main goal is to achieve near-perfection (aiming for 3.4 defects per million opportunities).
Principles
- Lean Manufacturing:
- Identify and eliminate the 7 types of waste (overproduction, waiting, transportation, over-processing, inventory, motion, and defects).
- Strive for continuous improvement (Kaizen).
- Promote a pull-based system (producing only what is needed when it’s needed).
- Six Sigma:
- Use a data-driven approach (DMAIC: Define, Measure, Analyze, Improve, Control).
- Focus on critical-to-quality (CTQ) metrics that impact customer satisfaction.
- Use statistical tools to analyze processes and eliminate variability.
Tools and Techniques
- Lean Manufacturing:
- Value Stream Mapping (VSM).
- 5S (Sort, Set in order, Shine, Standardize, Sustain).
- Kanban and Just-In-Time (JIT).
- Continuous flow and Takt time.
- Six Sigma:
- DMAIC methodology.
- Statistical Process Control (SPC).
- Fishbone Diagram (Ishikawa) for root cause analysis.
- Design of Experiments (DOE).
- Failure Modes and Effects Analysis (FMEA).
Focus Areas
- Lean Manufacturing: Addresses inefficiencies in processes that lead to delays, excess costs, or waste.
- Six Sigma: Addresses inconsistencies and defects in processes that lead to lower quality or customer dissatisfaction.
Metrics
- Lean Manufacturing: Measures efficiency improvements using metrics such as lead time, cycle time, inventory levels, and throughput.
- Six Sigma: Uses statistical measures like defect rates (DPMO), process capability (Cp, Cpk), and sigma levels.
Cultural Approach
- Lean Manufacturing: Encourages a culture of employee involvement and empowerment. Teams work together to identify and eliminate waste.
- Six Sigma: Often involves expert roles like Green Belts, Black Belts, and Master Black Belts who lead projects and drive change based on data.
Industries and Applications
- Lean Manufacturing: Primarily associated with manufacturing but increasingly applied to service industries, healthcare, and logistics.
- Six Sigma: Widely used in manufacturing, but also extensively adopted in finance, healthcare, IT, and other sectors where reducing defects and variability is critical.
Differences in Approach
- Lean Manufacturing: Emphasizes improving process flow and speed by removing waste and improving system efficiency.
- Six Sigma: Relies heavily on statistical analysis and root cause identification to improve process consistency and eliminate defects.
Common similarities:
- Both aim to improve processes and customer satisfaction.
- They can be integrated into a combined approach known as Lean Six Sigma, which balances speed and efficiency with quality and consistency.
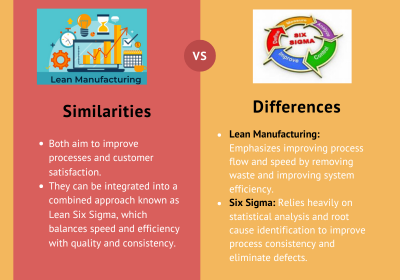
When to Use Each:
- Use Lean Manufacturing when the primary issues are inefficiencies, bottlenecks, or waste.
- Use Six Sigma when the primary issues involve defects, variability, or inconsistency in quality.
By combining the two approaches, organizations can address both efficiency and quality for comprehensive process improvement.