In this article, we discuss top 20 important HVAC technical interview questions with answers.
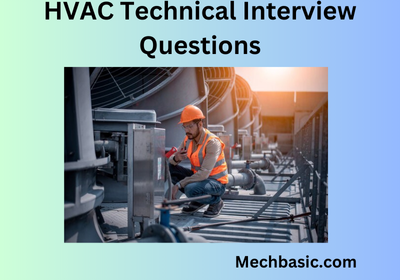
In this article
- Basic HVAC Concepts.
- Troubleshooting and Problem solving.
- System Design and Maintenance.
- Advanced HVAC Topics.
Basic HVAC Concepts.
1. Can you explain the refrigeration cycle and its main components?
The refrigeration cycle is the process by which heat is removed from one area and released into another, enabling cooling. It operates through four main components:
Compressor: Compresses low-pressure refrigerant gas into a high-pressure, high-temperature gas.
Condenser: Removes heat from the high-pressure gas, turning it into a high-pressure liquid.
Expansion Valve: Reduces the liquid’s pressure, cooling it significantly and converting it into a low-pressure, low-temperature liquid.
Evaporator: Absorbs heat from the indoor air as the low-pressure liquid evaporates into a gas, completing the cycle.
This cycle repeats continuously to provide cooling.
2. What is the difference between an air-cooled and a water-cooled condenser?
The main difference between air-cooled and water-cooled condensers lies in how they remove heat from the refrigerant:
- Air-Cooled Condenser: Uses ambient air (via fans) to cool and condense the refrigerant.
- Common Use: Smaller systems, such as residential AC units.
- Pros: Simple design, lower installation cost, less maintenance.
- Cons: Less efficient in hot climates.
- Water-Cooled Condenser: Uses water (via cooling towers or closed loops) to cool and condense the refrigerant.
- Common Use: Large commercial and industrial systems.
- Pros: Higher efficiency, works better in high ambient temperatures.
- Cons: Higher cost, requires water and regular maintenance.
3. How do heat pumps work, and in what scenarios are they most effective?
Heat pumps transfer heat from one place to another using electricity. In heating mode, they extract heat from the outside air, ground, or water and move it indoors. In cooling mode, they reverse the process, removing heat from indoors to cool the space.
Effectiveness:
- Mild climates: Best in areas with moderate temperatures, as extreme cold can reduce efficiency.
- Well-insulated spaces: Work optimally in buildings with good insulation.
- Versatility: Ideal for year-round use since they provide both heating and cooling.
4. What are the differences between R-22 and R-410A refrigerants? Why is R-410A preferred today?
Key Differences Between R-22 and R-410A:
- Chemical Composition:
- R-22 is a hydrochlorofluorocarbon (HCFC) with ozone-depleting properties.
- R-410A is a hydrofluorocarbon (HFC) and does not deplete the ozone layer.
- Environmental Impact:
- R-22 contributes to ozone depletion and has a higher global warming potential (GWP).
- R-410A has no ozone depletion potential but still has a lower GWP compared to R-22.
- Operating Pressure:
- R-410A operates at higher pressures than R-22, requiring specially designed equipment.
- Energy Efficiency:
- R-410A is more energy-efficient and provides better heat transfer performance.
Why R-410A Is Preferred Today:
- Environmental Regulations: R-22 production was phased out due to its ozone-depleting effects, as per the Montreal Protocol.
- Improved Performance: R-410A systems are more efficient, reliable, and eco-friendly.
- Compatibility: New HVAC systems are designed specifically for R-410A’s higher operating pressures and performance.
5. What does SEER (Seasonal Energy Efficiency Ratio) mean, and how does it affect HVAC performance?
SEER (Seasonal Energy Efficiency Ratio) measures the cooling efficiency of an HVAC system over a typical cooling season. It is calculated as the total cooling output (BTUs) divided by the total energy consumed (watt-hours).
Impact on HVAC Performance:
- Higher SEER = Greater Efficiency: Systems with higher SEER ratings use less energy to provide the same cooling, reducing utility costs.
- Comfort and Performance: High-SEER systems often include advanced features like variable-speed compressors, improving temperature control and comfort.
- Cost Considerations: High-SEER units have higher upfront costs but lower operating costs over time.
In essence, SEER helps gauge energy efficiency and long-term savings of an HVAC system.
Troubleshooting and Problem Solving
6. What steps would you take to troubleshoot an air conditioning unit that isn’t cooling properly?
To troubleshoot an air conditioning unit that isn’t cooling properly, follow these steps:
- Check the Thermostat Settings: Ensure it’s set to “cool” mode and the temperature is set correctly.
- Inspect the Air Filter: A dirty filter can restrict airflow and reduce efficiency. Clean or replace it if necessary.
- Examine the Evaporator Coils: Check for dirt or ice buildup. Clean or defrost if needed.
- Inspect the Condenser Unit: Ensure it’s free from debris and has proper airflow.
- Check Refrigerant Levels: Low refrigerant can affect cooling performance. If levels are low, call a professional for a refill.
- Verify the Airflow: Check for blockages in ducts and ensure vents are open and unblocked.
- Test the Circuit Breaker: Ensure the AC unit is receiving power by checking the breaker panel.
7. What could cause a furnace to short cycle, and how would you fix it?
Causes of Furnace Short Cycling:
- Clogged Air Filter: Restricts airflow, causing the furnace to overheat and shut off prematurely.
- Thermostat Issues: A faulty or miscalibrated thermostat can signal the furnace to shut down too early.
- Dirty Flame Sensor: A dirty or malfunctioning flame sensor can shut off the furnace for safety reasons.
- Overheating: Blocked vents, a dirty blower, or malfunctioning components can cause the furnace to overheat and turn off.
- Improper Size: An oversized furnace can heat the home too quickly, causing it to short cycle.
How to Fix It:
- Replace or Clean the Air Filter: Ensure proper airflow.
- Calibrate or Replace the Thermostat: Check settings and functionality.
- Clean the Flame Sensor: Carefully clean the sensor with a soft cloth.
- Inspect Vents and Ducts: Ensure there are no blockages.
- Check Furnace Size: Consult a professional to verify if the furnace size is appropriate for your home.
8. If an HVAC system has uneven heating or cooling, what could be the potential causes?
Uneven heating or cooling in an HVAC system can be caused by several factors:
- Blocked or Closed Vents: Closed or obstructed vents in certain rooms can restrict airflow and result in uneven temperature distribution.
- Dirty or Clogged Air Filter: A clogged air filter reduces airflow and can cause temperature imbalances throughout the system.
- Ductwork Issues: Leaky, poorly insulated, or improperly sized ducts can cause uneven airflow, leading to certain areas being too hot or too cold.
- Thermostat Placement: If the thermostat is located in a drafty area or near a heat source, it might inaccurately regulate the temperature, causing uneven heating/cooling.
- Improperly Sized HVAC System: An undersized or oversized system can struggle to maintain even temperatures. An oversized system might cool or heat too quickly, while an undersized system might struggle to reach the desired temperature.
- Dirty or Blocked Coils: Dirty evaporator or condenser coils can hinder heat exchange, affecting overall system efficiency.
- Zoning System Malfunctions: If the HVAC system uses zones for temperature control, a malfunctioning zone control system or damper could lead to uneven temperatures.
- Insufficient Insulation: Poor insulation in certain areas can cause heat loss or gain, affecting the overall temperature balance.
9. What do you do if a compressor fails to start, but the rest of the system is functional?
If a compressor fails to start but the rest of the system works, follow these steps:
- Check the Power Supply: Ensure the unit is receiving adequate power and that circuit breakers or fuses aren’t tripped.
- Inspect the Capacitor: A faulty capacitor may prevent the compressor from starting. Replace if needed.
- Test the Start Relay: A malfunctioning start relay can stop the compressor. Replace it if defective.
- Examine the Thermostat: Ensure it is functioning correctly and signaling the compressor to start.
- Check for Overheating: Allow the compressor to cool if it’s overheated, and verify proper airflow around the outdoor unit.
- Inspect Refrigerant Levels: Low refrigerant may prevent the compressor from engaging. Call a professional to assess and refill.
- Look for Mechanical Issues: Internal damage, like seized parts, may require compressor replacement.
10. How would you diagnose and repair a refrigerant leak?
Diagnosing a Refrigerant Leak:
- Check for Symptoms: Look for reduced cooling, hissing sounds, or ice buildup on coils.
- Visual Inspection: Inspect refrigerant lines, connections, and coils for visible damage or oil residue.
- Use Leak Detection Tools:
- Electronic Leak Detector: Detects refrigerant gas.
- UV Dye Test: Injects dye into the system to spot leaks under UV light.
- Soap Bubble Test: Applies soapy water to suspected areas to reveal bubbles from escaping gas.
Repairing a Refrigerant Leak:
- Seal Small Leaks:
- Use an appropriate sealant for minor leaks (if approved by the manufacturer).
- Replace Damaged Components:
- For larger leaks, replace faulty parts like coils, fittings, or lines.
- Recharge the System:
- Once repaired, evacuate the system, check for vacuum integrity, and recharge it with the correct type and amount of refrigerant.
- Test the System:
- Verify proper operation and confirm no further leaks.
System Design and Maintenance
11. How do you calculate the heating and cooling load for a building?
To calculate the heating and cooling load for a building, follow these steps:
- Gather Building Information:
- Floor area, ceiling height, number of rooms.
- Insulation levels, window sizes, and types.
- Building orientation and local climate data.
- Heat Gain/Loss Sources:
- External: Solar radiation, outdoor temperature.
- Internal: Occupants, appliances, lighting.
- Use a Standard Methodology:
- Apply industry-standard tools like Manual J from ACCA for precise calculations.
- Alternatively, use basic formulas for heat transfer through walls, windows, and roofs:
Q = U × A × ΔT, where:- Q = Heat transfer (BTUs/hour).
- U = Thermal transmittance (inverse of R-value).
- A = Surface area.
- ΔT = Temperature difference.
- Account for Ventilation:
- Factor in fresh air requirements and infiltration rates.
- Sum Total Loads:
- Combine all heat gains and losses to determine total heating and cooling requirements.
- Consider Safety Margins:
- Add a buffer to account for extreme weather or future needs.
For accurate results, software like HVAC load calculators or consulting a professional is recommended.
12. What is the purpose of a Variable Air Volume (VAV) system, and how does it differ from a Constant Air Volume (CAV) system?
Purpose of a Variable Air Volume (VAV) System:
A VAV system adjusts the airflow to different zones in a building based on demand, maintaining consistent temperature while optimizing energy efficiency. It provides precise control over heating, cooling, and ventilation, improving comfort and reducing energy consumption.
Differences Between VAV and Constant Air Volume (CAV) Systems:
Feature | VAV System | CAV System |
---|---|---|
Airflow | Adjusts airflow to meet zone demand. | Provides constant airflow at all times. |
Energy Efficiency | More efficient by reducing fan energy use. | Less efficient due to fixed airflow. |
Comfort | Better temperature control by zone. | Uniform temperature across all zones. |
Application | Ideal for buildings with varying loads. | Suitable for small or simple spaces. |
VAV systems are preferred in modern HVAC designs for their flexibility and energy savings.
13. How often should air filters be replaced, and why is it important for system efficiency?
How Often to Replace Air Filters:
- Standard filters: Every 1–3 months.
- High-efficiency filters: Every 6–12 months, depending on usage.
- Factors affecting frequency: Pets, allergies, and high system use may require more frequent replacement.
Why It’s Important:
- Improves Efficiency: Clean filters ensure proper airflow, reducing strain on the system.
- Enhances Air Quality: Removes dust, allergens, and pollutants from the air.
- Prevents Damage: Reduces wear and tear on components like the blower and compressor.
- Saves Energy: A clean filter can lower energy consumption by up to 15%.
Regular filter replacement is crucial for performance, longevity, and indoor air quality.
14. What is the role of dampers in an HVAC system? How do you adjust them for optimal performance?
Role of Dampers in an HVAC System:
- Control Airflow: Regulate the volume and direction of air to different zones or rooms.
- Balance the System: Ensure even heating, cooling, and ventilation throughout the building.
- Zoning: Enable independent temperature control in specific areas when used in zoning systems.
Adjusting Dampers for Optimal Performance:
- Locate the Dampers: Typically found in the ductwork near the HVAC unit.
- Adjust Seasonally: Open dampers for rooms requiring more airflow and partially close others as needed.
- Balance Airflow:
- Use trial and error to balance airflow across all rooms.
- Avoid fully closing dampers to prevent pressure buildup in the system.
- Mark Positions: Once balanced, mark damper positions for easy future adjustments.
Proper damper adjustment enhances comfort, efficiency, and HVAC performance.
15. What is the importance of ductwork design, and what issues can arise from poorly designed ducts?
Importance of Ductwork Design:
- Efficient Airflow: Proper design ensures even distribution of heated or cooled air throughout the building.
- Energy Efficiency: Minimizes air leaks and resistance, reducing energy consumption.
- Comfort: Maintains consistent temperatures and airflow in all zones.
- System Longevity: Reduces strain on the HVAC system, preventing premature wear.
Issues from Poorly Designed Ducts:
- Uneven Temperatures: Leads to hot or cold spots in different areas.
- Increased Energy Costs: Air leaks and high resistance waste energy.
- Reduced Air Quality: Leaks can introduce dust and contaminants into the system.
- System Strain: Poor airflow increases workload on the HVAC unit, reducing its lifespan.
- Noise: Improper sizing or layout can cause whistling, rattling, or other noises.
Proper duct design is essential for efficiency, comfort, and long-term HVAC performance.
Advanced HVAC Topics
16. What is the difference between a single-stage, two-stage, and variable-speed compressor?
- Single-Stage Compressor:
- Operation: Operates at full capacity (on) or not at all (off).
- Efficiency: Least efficient due to frequent cycling.
- Comfort: Provides basic temperature control, with less precise comfort.
- Use: Ideal for small spaces or moderate climates.
- Two-Stage Compressor:
- Operation: Runs at two levels—low for mild conditions and high for extreme conditions.
- Efficiency: More efficient than single-stage, as it adjusts output to demand.
- Comfort: Provides better temperature consistency and humidity control.
- Variable-Speed Compressor:
- Operation: Adjusts speed continuously to match exact cooling or heating needs.
- Efficiency: Most efficient, minimizing energy use and cycling.
- Comfort: Offers the most precise temperature control and excellent humidity management.
- Use: Ideal for larger homes or areas with extreme weather variations.
17. How does a Building Management System (BMS) or Direct Digital Control (DDC) system integrate with HVAC systems?
Integration of BMS/DDC with HVAC Systems:
- Monitoring: BMS/DDC systems continuously monitor HVAC components (e.g., temperature, humidity, airflow) using sensors.
- Control: Automate and adjust HVAC operations, such as starting/stopping equipment, regulating airflow, or modulating temperatures, based on real-time data.
- Energy Efficiency: Optimize energy use by scheduling, zoning, and adjusting setpoints to match occupancy and building needs.
- Fault Detection: Identify and alert for equipment malfunctions or inefficiencies, enabling proactive maintenance.
- Integration: Connect with other building systems (lighting, security) for comprehensive building management.
Key Benefit:
BMS/DDC systems enhance HVAC efficiency, reduce energy costs, and improve occupant comfort by providing centralized, automated control.
18. Can you explain how geothermal HVAC systems work? What are their benefits and drawbacks?
How Geothermal HVAC Systems Work:
- Principle: Geothermal systems use the stable temperature of the earth to heat and cool a building. A loop of pipes (either vertical or horizontal) is buried in the ground, circulating a fluid that absorbs or releases heat from the earth.
- Heating: In winter, the system extracts heat from the ground and brings it into the building.
- Cooling: In summer, the system reverses the process, transferring heat from the building into the cooler ground.
Benefits:
- Energy Efficiency: Geothermal systems are highly efficient, offering up to 4 times the energy output compared to input.
- Environmentally Friendly: Uses renewable energy from the earth, reducing greenhouse gas emissions.
- Long Lifespan: The ground loop can last 50+ years, and the heat pump typically lasts 25+ years.
- Lower Operating Costs: Reduced energy consumption leads to lower utility bills over time.
Drawbacks:
- High Initial Cost: Installation is expensive due to the need for drilling or trenching.
- Space Requirements: Requires ample land for horizontal loops or space for vertical drilling.
- Long Payback Period: While energy savings are significant, the initial cost can take years to recover.
19. What are the safety measures you take when handling high-voltage equipment and refrigerants?
Safety Measures for Handling High-Voltage Equipment:
- Turn Off Power: Always ensure the power is turned off before working on high-voltage equipment.
- Use Proper PPE: Wear insulated gloves, safety glasses, and protective gear.
- Test for Voltage: Use a voltage tester to confirm no power is present before touching components.
- Follow Lockout/Tagout Procedures: Use lockout/tagout to prevent accidental power restoration.
- Stay Dry: Avoid working in damp or wet conditions to reduce the risk of electrical shock.
Safety Measures for Handling Refrigerants:
- Wear PPE: Use gloves, goggles, and a long-sleeve shirt to prevent skin contact with refrigerants.
- Proper Ventilation: Ensure the work area is well-ventilated to avoid refrigerant buildup, which can displace oxygen.
- Use Correct Equipment: Only use gauges, hoses, and tools rated for refrigerant pressure and compatibility.
- Check for Leaks: Regularly check for refrigerant leaks using proper detection methods.
- Avoid Direct Contact: Do not allow refrigerant to come into direct contact with skin to prevent frostbite.
Following these safety protocols ensures safe handling of both high-voltage equipment and refrigerants, minimizing the risk of injury or system damage.
20. How do you balance energy efficiency and performance when designing or maintaining an HVAC system?
Balancing Energy Efficiency and Performance in HVAC Design/Maintenance:
- System Sizing: Ensure the HVAC system is appropriately sized for the building’s needs. An oversized or undersized system can lead to inefficiency and poor performance.
- Proper Insulation: Insulate ducts and ensure proper building insulation to reduce heat loss/gain, which improves energy efficiency and supports consistent performance.
- Efficient Equipment: Choose energy-efficient equipment (e.g., high SEER, Energy Star-rated units) to reduce energy consumption while maintaining effective cooling/heating.
- Zoning Systems: Implement zoning to condition only the areas that need it, improving energy use while enhancing comfort.
- Regular Maintenance: Clean filters, check refrigerant levels, and inspect ducts to ensure the system runs smoothly and efficiently.
- Smart Controls: Use programmable thermostats or BMS/DDC systems to optimize energy use based on occupancy and external conditions while ensuring optimal comfort.
By balancing efficient equipment, correct sizing, regular maintenance, and intelligent control, you can achieve both energy savings and effective performance.