Preparing a DXF file for machining in SolidWorks involves a series of steps to ensure that the file is correctly formatted, contains accurate geometry, and is optimized for CNC machining. Here’s a step-by-step guide:
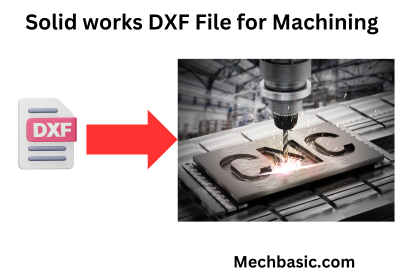
In this article
- What is as DXF File in Solid works?
- Consequences of Poor DXF File
- Steps to prepare a DXF File for Machining.
What is a DXF File in Solid works?
A DXF file (Drawing Exchange Format) in SolidWorks is a file format used to represent 2D and 3D design data. It is commonly used for sharing and exporting designs between CAD programs and is widely supported by CNC machining, laser cutting, and other manufacturing tools.
In SolidWorks, DXF files are typically created to share flat 2D representations of a part or assembly and are essential for processes like CNC cutting, engraving, or manufacturing.
Consequences of Poor DXF File
A poorly prepared DXF file can lead to various issues during CNC machining, affecting the final quality of the machined part, productivity, and cost. Here are the consequences of a poor DXF file:
- Machining Errors.
- Increased Machining Time
- Tool Breakage or Damage.
- Waste of Material.
- Production Delays
- Poor Surface Finish.
- Miscommunication with Machinist.
Steps to prepare a DXF File for Machining:
Here are the step by step procedure to create a proper DXF file from Solid works.
1. Create or Open the Part/Assembly
- Open your part or assembly in SolidWorks.
- Ensure that the design is finalized and matches the machining requirements (e.g., material, dimensions, tolerances).
2. Generate a 2D Drawing (Optional for Flat Parts)
- If the part is flat or requires 2D machining:
- Go to File > Make Drawing from Part/Assembly.
- Select the appropriate drawing template.
- Place the desired views (e.g., top view) onto the drawing sheet.
3. Prepare the Sketch for Export
- If working with a 3D model, identify the face or features you want to export for machining.
- Create a 2D sketch on the required face or plane, and fully define it.
- Ensure the sketch contains only the required machining geometry (e.g., contours, holes).
4. Simplify the Geometry
- Remove any unnecessary features, such as annotations, hidden lines, or construction geometry, that are not required for machining.
- Ensure all lines are connected and there are no gaps or overlaps in the geometry.
5. Export as DXF
- Go to File > Save As.
- In the “Save as type” dropdown, select DXF (*.dxf).
- In the DXF Export Options dialog:
- Select Geometry: Choose the face, view, or sketch you want to export.
- Enable Export all splines as polylines (if required by your CNC software).
- Check options for scale to ensure the geometry is exported at the correct size.
- Preview the DXF file to verify accuracy.
6. Verify Layers and Line Types
- Use the DXF export options to assign layers and colors to different features (e.g., contours, holes, cut lines, or engravings).
- Match the layers and line types to your CNC machining software’s requirements.
- Ensure the file format and settings (e.g., units, polylines, and tolerances) are compatible with the CNC machine or CAM software.
- Communicate with your machinist or CNC operator to confirm any specific requirements.
8. Test the File
- Open the exported DXF file in a CAD viewer or the CNC machining software to verify:
- Accuracy of dimensions.
- Correct alignment and placement of features.
- Completeness of the machining geometry.
Tips for DXF Preparation in SolidWorks
- Unit Consistency: Verify the units (mm, inches) match the CNC requirements.
- Avoid Splines: Convert splines to polylines or arcs if the CNC software doesn’t support splines.
- Use Clean Geometry: Ensure there are no overlapping entities, duplicate lines, or open contours.
- Keep It Simple: Only include the essential features required for machining.
By following these steps, you can prepare an accurate and clean DXF file in SolidWorks that’s ready for CNC machining.