Ductwork plays a crucial role in air distribution within HVAC systems. Proper duct design and sizing ensure efficient airflow, energy savings, and occupant comfort.
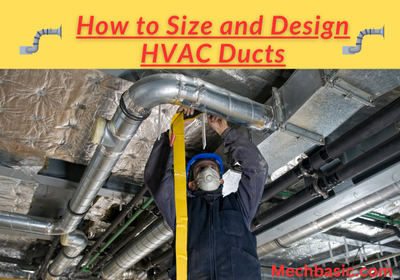
In this article:
What is a Duct in HVAC?
In HVAC, a duct is a passageway (usually made of metal, fiberglass, or flexible materials) that transports air for heating, ventilation, and cooling throughout a building. It ensures proper airflow and maintains indoor air quality and comfort.
Basics of a Good Duct Design:
- Airflow Requirements (CFM) – Ensure proper air supply for each room.
- Duct Material & Shape – Common types: rectangular, round, oval (round is most efficient).
- Friction & Pressure Loss – Minimize resistance using smooth, properly sized ducts.
- Static Pressure – Maintain proper 0.5″–0.8″ WC (inches of water column) for optimal system efficiency.
- Velocity (FPM – Feet Per Minute) – Balance between quiet operation and effective air movement.
Duct Sizing Methods
Proper duct sizing ensures efficient airflow, minimizes pressure losses, and maintains comfort while keeping energy consumption low.
Here are the most commonly used methods for duct sizing in HVAC systems:
- Equal Friction Method
- Velocity Reduction Method
- Static Regain Method
- Constant Velocity Method
- Total Pressure Method
Lets discuss each method in detail:
Equal Friction Method:
Keeps constant friction loss per unit length, balancing pressure drops across the system.
- The most commonly used method in HVAC design.
- Maintains a constant friction loss per unit length of ductwork (typically around 0.1 inches of water per 100 feet).
- Ensures a balanced pressure drop across different sections, leading to a uniform airflow distribution.
- Advantages:
- Simple to use and widely accepted.
- Works well for small to medium-sized systems.
- Disadvantages:
- May require dampers for fine-tuning airflow.
- Not ideal for very large or high-velocity systems.
Velocity Reduction Method :
Controls airspeed to reduce noise and turbulence, commonly used in low-pressure systems.
- Focuses on reducing airflow velocity in different sections to control noise and turbulence.
- High velocity is used near the fan, gradually decreasing as air moves through the system.
- Ensures quieter operation and reduces energy losses.
- Advantages:
- Effective for noise-sensitive environments (e.g., offices, hospitals).
- Reduces turbulence and pressure losses.
- Disadvantages:
- May require larger ducts, increasing installation costs.
Static Regain Method :
Ensures pressure recovery by increasing duct size after restrictions, used in large systems.
- Aims to recover pressure losses by increasing duct size after restrictions.
- Used mainly in high-velocity systems (e.g., large commercial buildings).
- Reduces energy losses by maintaining a near-constant total pressure.
- Advantages:
- Efficient for long duct runs and large-scale HVAC systems.
- Reduces the need for fan power adjustments.
- Disadvantages:
- More complex calculations and design process.
Constant Velocity Method :
Maintains a consistent air velocity, often applied in small-scale ductwork.
- Keeps a uniform airflow velocity throughout the duct system.
- Typically used in small-scale applications, such as residential HVAC systems.
- Prevents excessive noise and pressure drops by limiting high velocities.
- Advantages:
- Simple and easy to implement.
- Works well for low-pressure systems.
- Disadvantages:
- Not suitable for large, high-pressure systems.
- May lead to oversized ducts in some areas.
Total Pressure Method :
Balances both static and dynamic pressures for optimized performance
- Balances both static and dynamic pressure losses to optimize system efficiency.
- Used mainly in complex commercial and industrial HVAC designs.
- Ensures that air reaches each outlet efficiently with minimal losses.
- Advantages:
- Ensures high efficiency in large systems.
- Optimizes airflow distribution.
- Disadvantages:
- Requires detailed calculations and precise design.
- More complex than other methods.
Duct Shapes & Materials :
Duct Shape | Pros | Cons |
---|---|---|
Round | Most efficient, lowest friction | Needs more space |
Rectangular | Easier to fit in ceilings | Higher friction & pressure loss |
Oval | Hybrid between round & rectangular | More expensive |
🔹 Material Choices:
- Galvanized Steel – Most durable, used in commercial systems.
- Flexible Ducts (Flex Ducts) – Easy to install, but high friction loss.
- Fiberglass Ductboard – Insulated, good for noise reduction.
- PVC & Aluminum – Used for special applications.
Common Duct Sizing Example
Example:
- 3-Ton AC (1,200 CFM) → Main Trunk Duct Needed
- Round Duct Size: 14″ diameter
- Rectangular Duct Size: 10″ x 14″
Branch Ducts (to individual rooms):
- Bedroom (200 CFM) → 8″ Round Duct
- Living Room (300 CFM) → 10″ Round Duct
Common Duct Problems & Fixes:
Problem | Cause | Solution |
---|---|---|
Low Airflow | Undersized ducts, high friction | Increase duct size, reduce bends |
Noisy Operation | High velocity, improper dampers | Use larger ducts, add dampers |
Uneven Cooling/Heating | Poor duct balancing | Install dampers, check CFM distribution |
High Static Pressure | Too many bends, restrictive filters | Reduce restrictions, increase duct size |
Conclusion:
Best Practices for Duct Design:
✔ Size ducts properly using Manual D or Equal Friction Method.
✔ Use round ducts when possible for best airflow efficiency.
✔ Keep velocity & static pressure in check to avoid noise & energy loss.
✔ Ensure proper balancing with dampers & registers.
Also Read:
Watch : How to design a Duct system.
Other Courses:


